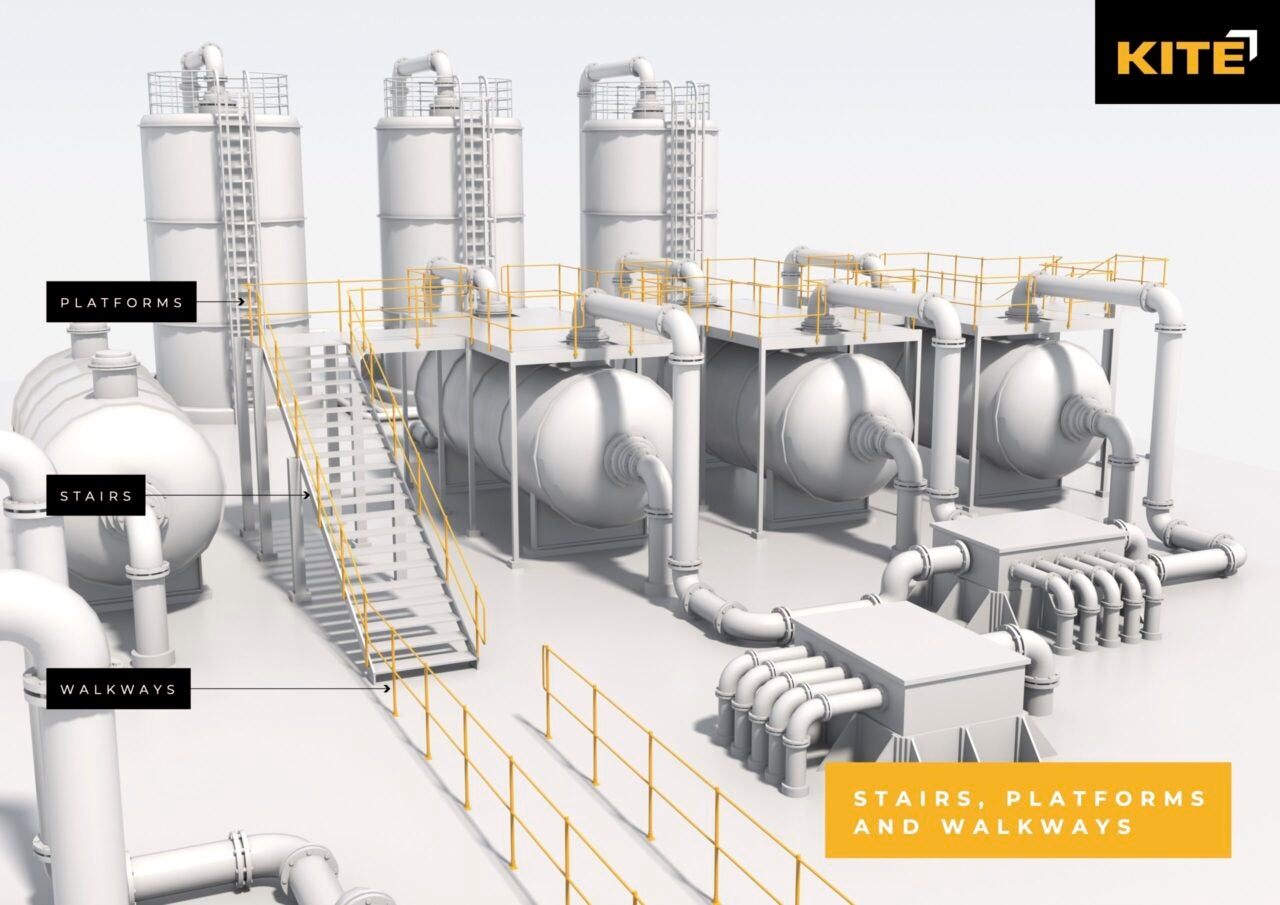
UK-based permanent handrail, walkway and barrier market leader Kite Group has developed new and improved handrails for railways across the UK, representing the first major innovation product since the 1930s.
Kite Group’s updated handrails and safety barriers aim to improve safety for millions of workers on the UK railways. The handrails, created via laser cutting technology, can be assembled without the need to use clamps or welding which not only saves time during production but also delivers environmental benefits as well.
Removing the clamps from the development process reduces the overall amount of steel needed, lowering production costs by 20% and significantly reducing the carbon footprint of the railings.
Frankie Youd speaks with company director Anthony J Wells to find out more about these new fixtures and the benefits that they bring with them.
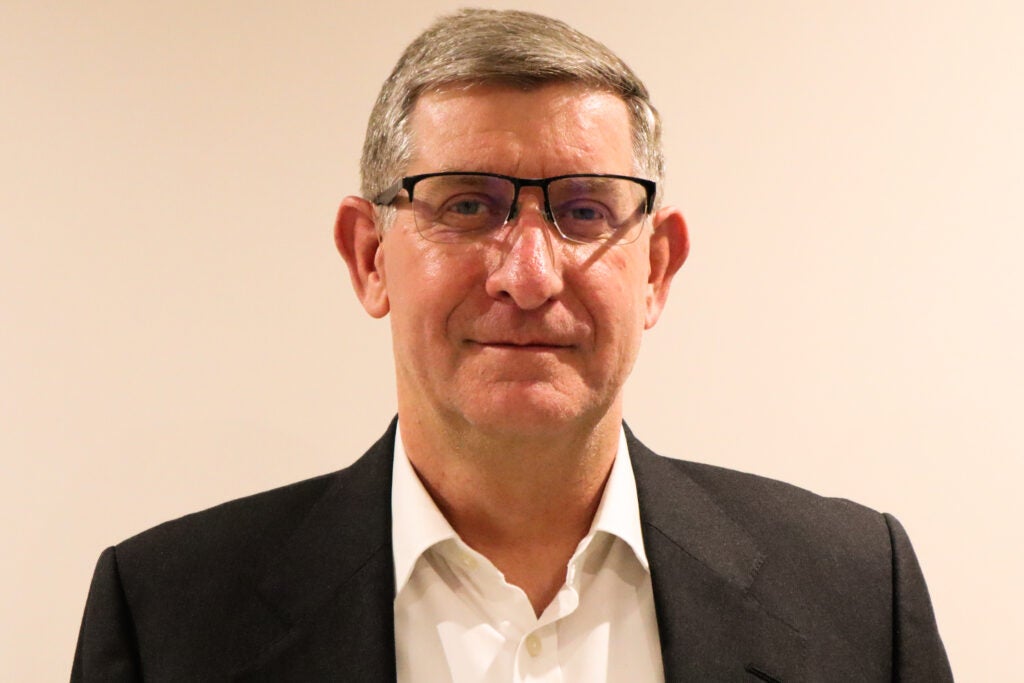
Frankie Youd (FY): Could you provide me with a bit of background on the company?
Kite was started as a partnership in 2003 in Edinburgh by David Holmes and his family, specialising in commercial and industrial handrailing systems and other permanent safe access system components.
Kite is very much a Scottish company supplying the oil and gas industry along with the numerous distilleries.
How well do you really know your competitors?
Access the most comprehensive Company Profiles on the market, powered by GlobalData. Save hours of research. Gain competitive edge.
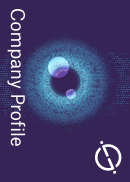
Thank you!
Your download email will arrive shortly
Not ready to buy yet? Download a free sample
We are confident about the unique quality of our Company Profiles. However, we want you to make the most beneficial decision for your business, so we offer a free sample that you can download by submitting the below form
By GlobalDataThe company grew steadily to 2015 when it became a limited company and his son joined with two other directors. The company has continued to progress up to 2020 when David, the founder, sadly passed away as an early victim of Covid-19.
After a difficult year, I joined the company in December 2020. Kite has a sister company in Winchester Kite Engineering and is now part-owned by CLD Fencing Systems one of the UK’s largest producers of mesh security fencing.
Could you explain the new handrails and safety barriers – what sets them apart?
The new handrail system is really set apart by its modern method of production, its cost efficiencies and green credentials whilst still fulfilling the primary purpose of assisting safe access and egress in industrial areas.
This method of handrail replaces Victorian type stick and ball posts that require individual parts to be made and welded together, whereas, with Modifix, the tubular uprights are simply cut using CNC [computer numerical control] laser machines.
Whilst this technology has been around for a long time, the cost for such simple products to be produced has been prohibited by the high cost of the machinery. This has been now developed and is far more economical to buy and run.
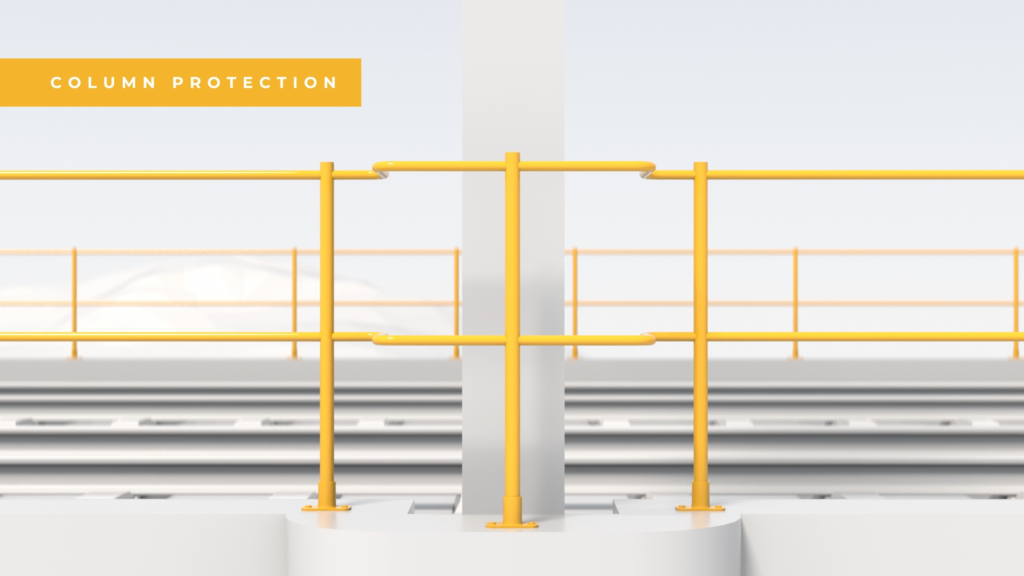
The alternative to the stick and ball is cast steel couplings which are, due to the antiquated method of production, primarily only produced in the East Asia which comes with a high environmental impact both in production and transport.
The great thing about this is that this system can be produced so much quicker with a massively reduced impact on the environment eliminating the hazards associated with welding at no extra cost.
What are the main benefits of the new fittings when it comes to safety?
The main benefit when it comes to safety is there are very few fittings that can come loose or points where sections could be inadvertently dismantled and removed. This system has been extensively tested in accordance with BS [British Standards] by [certification service provider] Lloyds British and performs better or equal to the time-served traditional systems.
The key benefits for the industry are product lead time, cost and versatility whilst having a modern clean appearance.
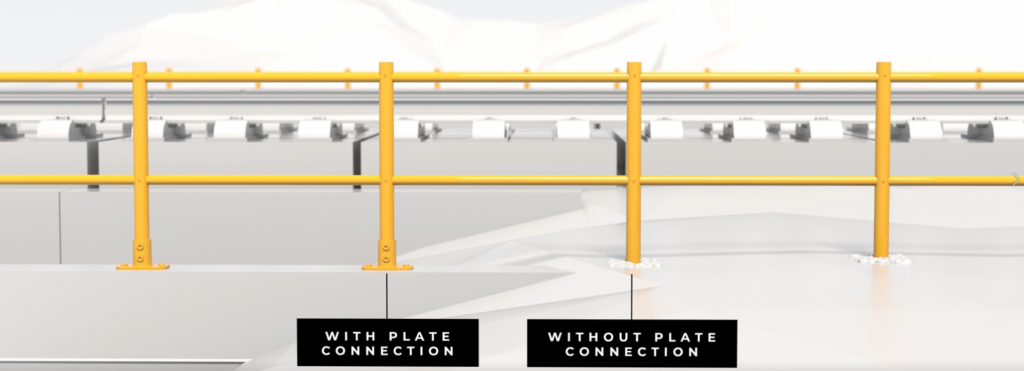
How do the new products deliver environmental benefits?
Firstly, there is no welding required so no harmful fumes compared with the stick and ball system and compared with the cast fitting systems as already mentioned these typically are made in the Far East and the carbon footprint as we all know is high.
Where are these products currently being used?
This product has only just been launched and so is currently being used in general industrial areas because typically utility and transport infrastructure companies are slow to change from traditional specifications.
Kite is now consistently looking for new opportunities to develop products that fulfil a traditional role and requirement but using modern methods and materials. Watch the space.