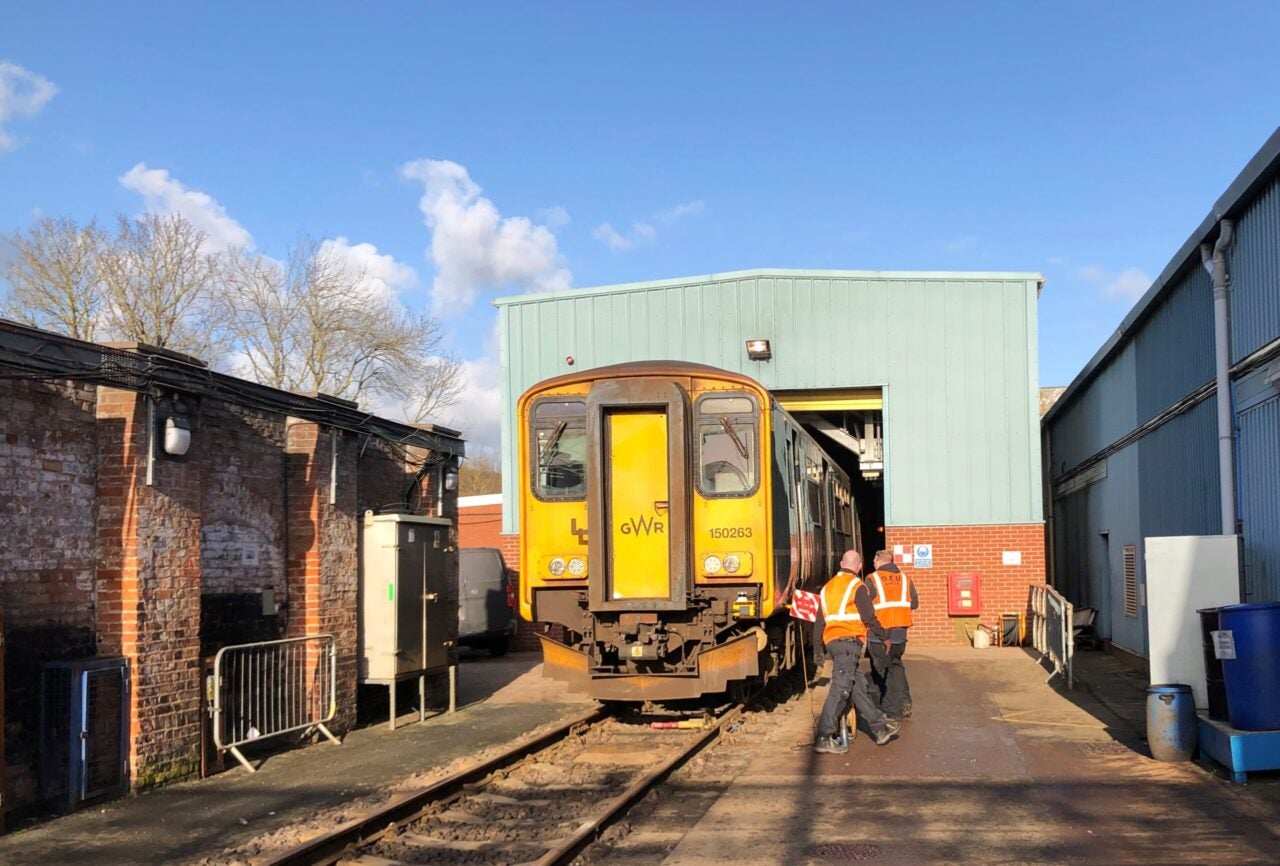
Thales has developed Robust Train Positioning System, a system that provides accurate train positioning data and a digital map of the track to improve the UK railway safety and efficiency.
Last month Thales introduced Robust Train Positioning System (RTPS) that aims to provide hyper-accurate train positioning data to further increase safety on UK railways.
The system aims to increase safety using a variety of sensors that collect critical data on train positioning, which is then combined with a digital map of the track, providing accurate and continuous positioning output for train drivers and other staff.
The new technology partners with the company’s existing Train Protection and Warning System (TPWS) that allows supervision to ensure the train stays within permitted speeds and movements.
The technology has been installed onboard a Great Western Rail 150 cab, marking the start of at least one year of data gathering to test and verify the technology. Supported by Network Rail and Great Western Rail, Thales will be in constant communication with the operators who will send in data for analysis.
Frankie Youd speaks to Thales’ product line manager Alex Stockill to find out more about the new technology and its benefits.
How well do you really know your competitors?
Access the most comprehensive Company Profiles on the market, powered by GlobalData. Save hours of research. Gain competitive edge.
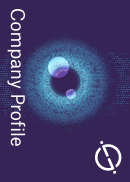
Thank you!
Your download email will arrive shortly
Not ready to buy yet? Download a free sample
We are confident about the unique quality of our Company Profiles. However, we want you to make the most beneficial decision for your business, so we offer a free sample that you can download by submitting the below form
By GlobalData
Frankie Youd (FY): How does the RTPS technology work?
Alex Stockill (AS): The RTPS equipment is composed of a range of sensor systems, collating inputs from all sensors and combining them with a digital map of the track to provide an accurate and continuous positioning output.
By combining this system with existing Train Protection and Warning System (TPWS) technology, the train can be supervised against permitted movements and speeds and activate the emergency brake in the event of a ‘signal passed at danger’ (SPAD) or excess speed incident.
What are the benefits of RTPS?
Access to both position and speed, alongside a driver interface and emergency brake, via TPWS.
A very wide range of new applications can be deployed quickly and at a low cost. Some key examples are continuous overspeed protection and user-worked crossing safety enhancements. This can be achieved without a requirement for new trackside infrastructure.

How does TPWS work alongside and complement RTPS?
The current TPWS protection works on powered grids at specific points of the track to stop the train if it approaches a red signal too quickly, or upon passing a red signal. The new system effectively upgrades” TPWS and turns the entire track into a virtual continuous power grid.
This will enhance safety trackside by allowing continuous communications and early warning of red signals and obstructions anywhere on the network, such as track maintenance and repairs. It also enables driver warnings to be provided via the existing TPWS driver interface.
Can this technology be retrofitted onto any train cab?
Yes, it is of a much smaller footprint than other comparable systems and the re-use of TPWS hardware minimises retrofit effort. There is minimal requirement to change the cab desk as the solution re-uses the TPWS DMI.
Does it require any additional software or training?
The existing software utilised in trials is not yet product ready and a development effort is required to achieve railway standards.
Training is dependent on the use case, but using the TPWS integration example, re-use of familiar warnings and interfaces to the drivers will minimise training efforts required.
Where will the trials be carried out, are there plans for further development?
Currently, the train is continuously gathering data as it runs in passenger service, effectively a very long trial with a wide coverage area.
There are live trials planned at locations in the Southwest. An early prototype was used to provide a successful proof of concept test at ENIF [European Train Control System National Integration Facility] in 2020.
Why do you think that technology such as this has not been implemented into the rail industry sooner?
The technology has developed out of a need for industry to address the concern of increasing SPADS and delays to ETCS roll out. It’s a great example of industry working collaboratively to solve performance and safety issues now and provide a migration path to full ETCS as planned.
The number of use cases and convenience of a system like this certainly has the potential to become a key staple across all rolling stock in the future of UK rail.