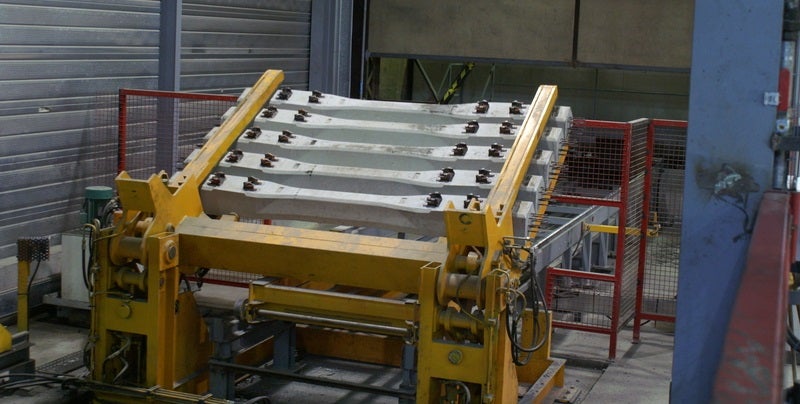
Advanced Precast Systems (APS) designs and manufactures steel formworks for concrete units, as well as provides clients with an industrial plant to produce these elements on a large scale.
The company specialises in global solutions for the production of railway sleepers, slab tracks, breakwaters, noise panels and housing. Each project APS follows offers fully customised products, tailored to the needs of the client.
Steel moulds for pre-stressed sleepers and concrete slab tracks
APS manufactures steel moulds for pre-stressed railway sleepers and concrete slab tracks.
To produce these pre-stressed concrete sleepers, steel cables are tightened and placed in the moulds before the casting phase. Once the concrete is dry, they will naturally return to their initial size, ensuring both a tight lock and the required material strength. This special process requires the resilient auto-resistant steel moulds that APS provides; their use ensures that the final product is of consistent quality.
APS also manufactures classic, post-stressed sleeper moulds, as well as slab track moulds, which deliver another concrete product with the same properties. An alternative solution to sleepers, slab tracks can fill the same role and sometimes represent a better alternative in some circumstances.
Automated plants to mass produce railway products
In order to produce these railway sleepers, two options are usually available; the long line system or the carousel. Due to the growing need for customised solutions and better cost efficiency, APS customers tend to increasingly favour the carousel, as it requires less space and fewer people on-site, as well as offers better adaptability to settings, and delivers higher quality products.
Automated carousels are divided into three lines: working, curing and evacuation. Sleeper moulds are positioned on a plate that glides on conveyors in order to transfer them automatically from one work station to the next one, ensuring an important time gain.
Once the sleepers are demoulded, they are transferred on the evacuation line in order to add accessories, such as rail pads and toe insulators, before being stored. APS can design special machines which can be included at any stage of the production process within the carousel, and which will automate part of it.
A typical automated carousel produces 640 sleepers over eight hours, with seven people in total working in the plant, as opposed to a long line system which needs twice as many people. Carousels can be adapted to an existing structure, or be built from scratch. They can also be upgraded as the project unrolls, starting small then adding more modules to the carousel, in order to deliver more products if necessary.
Custom-made precast solutions
A brand of CBE Group, one of the world’s leaders in mould, equipment and precast facilities for concrete tunnel segments, APS closely accompanies its clients through all phases of their project, from the pre-project study and production, to the set-up of the factory on-site by a dedicated technical team.
APS also designs, manufactures and assembles all necessary parts and equipment in order to produce smooth and firm concrete units that correspond exactly to the requirements of the project and client.