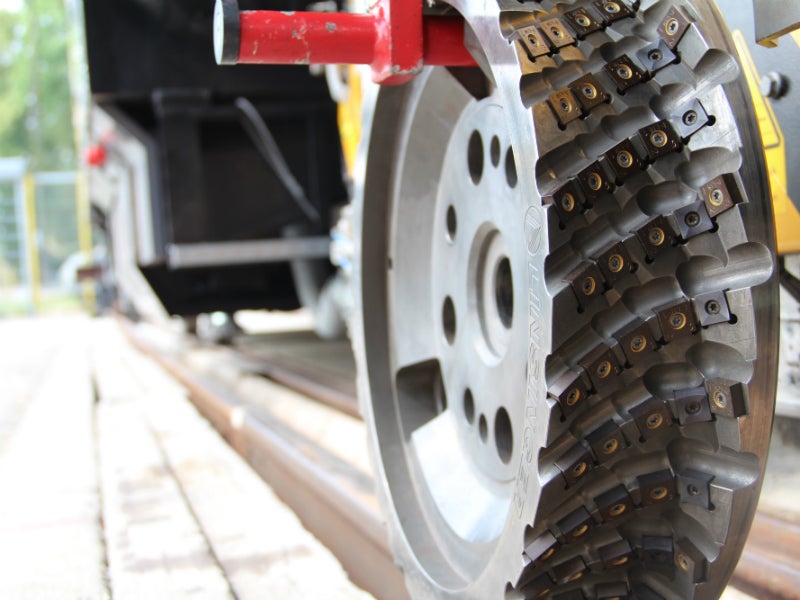
The rising pressure in rail traffic needs modern and reliable Linsinger rail milling technology in order to prolong railway life and reduce service disrupting interventions.
Higher train frequencies, more kilowatts of power and increased torque input lead to faster development of rail defects. This combined with reduced track access time reduce the applicability for multi-pass rail processing methods.
In addition, the risk of fire, track debris, grinding dust, high volumes of exhaust gas, as well as changes to metallurgical structure of the rail represent side effects of traditional rail maintenance technologies.
Compared to other maintenance methods, the rail milling process introduces hardly any heat into the railhead and completely prevents operator related profile variability.
When milling in dedicated track possessions, no forced work exclusion zone is created and as a result, other track personnel can safely use the same time window / track possession for other valuable track and red zone work. This advantage clearly increases the value of track access time.
By switching to Linsinger rail milling with, pre and post treatment asset condition recording, infrastructure owners, as well as train operators, can immediately benefit from key advantages of this maintenance technology, regeneration of the rail head surface and restoration of the desired target profile (subject to suitability of the rail). This can in some cases add up to 12 years of rail life extension.
“Imagine, depending on the rail condition, up to 12 years of life extension in one pass deferring capital expenditure, releasing resources for critical renewal and replacement, and at the same time enabling people working on the track, signals and other assets in the same work area.”
Challenges in the system
Rising number of passengers, smaller train intervals, and growing freight volume all pose high demands on vehicles and rails. Infrastructure owners and train operators face the impact of rail defects arising faster due to these increased demands and at the same time face the challenge of less time for maintenance due to reduced track access time.
Despite improved rail quality, classic defects like profile deformation, wear, long and short-wave corrugation or rolling contact fatigue (RCF) occur due to these increased loading conditions.
With respect to RCF defects, the focus is put on periodic cracks on the gauge corner, so-called head checks. After initial slow growth, these cracks will grow exponentially and can lead to spalling on the gauge corner if not treated in time. If left completely untreated head checks can result in catastrophic rail failures.
Other critical defects are squats (also called studs or squat type defects). As these defects don’t show the same classic RCF crack growth behaviour, they can reach depths of 8mm – 10mm very quickly (within 10 million tonnes to 30 million tonnes of load) and can cause extensive spalling-like surface break-outs.
Until now, no rail breaks through squat type defects have been recorded. However, they can lead to “secondary” rail breaks through dynamic overloading in combination with other defects, for example, head checks.
Apart from rail defects, noise pollution caused by rail traffic is a central topic, especially in urban areas. Singular sources of noise on rails such as welds, wheel burns, as well as periodical sources such as corrugation can lead to a great social and political pressure on infrastructure providers requiring compensation payments to residents.
Moreover, higher dynamic pressure and vibration in various frequency ranges induced by these ‘noise points’ can also lead to reduced durability of rail fastenings, ballast degradation and damage to other structures and components, as well as an increased degradation rate of track geometry.
Modern high-performance milling technology
LINSINGER has been extensively engaged with milling technology for more than 60 years. In the first 30 years of business, Linsinger focused on stationary milling plants. Then, an innovative technological breakthrough was achieved in the mid-90s with the introduction of the first mobile rail milling train.
In the last 20 years, through extensive experience with over 50 active machines and dedicated research and development, the high-performance milling technology was developed. This technology will, for example, soon be used in the new MG31 high-performance milling train for Crossrail (Transport for London) in the UK.
Linsinger high-performance milling technology uses circumferential milling that can rebuild transversal and longitudinal profile within the smallest tolerance and remove all surface defects in just one pass. As this is a rotational cutting process, only milling chips (and no dust, no sparks) are produced, which are stored in the chip storage on the machine for later recycling.
Extensive tests showed that rotational milling is the most suitable technology for mobile rail milling due to productive and technological reasons. Furthermore, extensive development has been put into cutter heads to increase precision, speed, tool life and productivity. Research has shown that too small, as well as too big, cutter heads have a negative impact on tool life and increase maintenance costs.