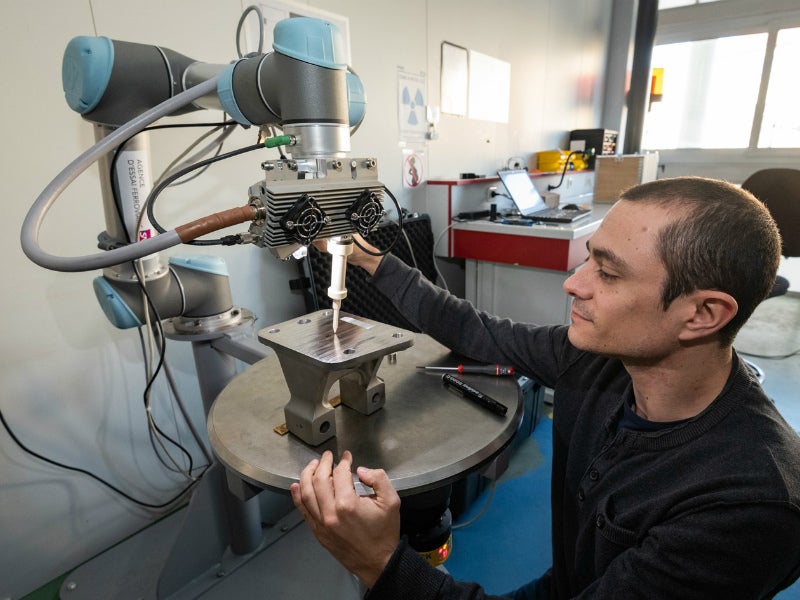
Railway maintenance laboratories may be required to provide results for resistance testing carried out on parts to various stresses using fatigue tests.
However, it is possible to go even further and determine the level of stress suffered by a part in operation. This entails studying the signs left by forces when the part has cracked.
There are three major challenges to this determination of stress:
- Establishing the role of the load in the failure
- Defining how long it has been since the crack appeared
- Defining the remaining service life (time before the part breaks)
This issue has been the subject of a research programme at the Railway Testing Agency (AEF), a laboratory partner of Eurailtest. The method developed consists of studying the fracture in a mechanical part. This involves analysing those fractures in order to obtain a profile of deep residual stress changes.
This innovative testing method is based on X-Ray Diffraction (XRD) analysis. The AEF has recently invested in a new X-ray diffractometer, the X-RayBot. This investment ensures better performance and accuracy during analysis.
Additionally, this device is portable and can be transported to a given site. This was done last summer, with measurements on TGV power cars taken at the maintenance centre.
An AEF client had a fatigue test conducted on a wheel after failures occurred on a series of parts. The laboratory’s experts offered the client an additional service, an innovative one tailored to its needs, which involved determining the load experienced in operation using the method developed at the AEF. This study was carried out on a wheel, with XRD analyses, first on the surface and then in depth, on the fracture.
Results were conclusive and seen as high-quality by the client, who is in favour of continuing analysis in greater detail
This new method, still in development, makes it possible to respond to a client’s need regarding maintenance and to limit the corresponding costs. This method may be used in support of the fatigue tests conducted at the AEF.
The AEF is currently the only laboratory to offer this type of service. It will be presented at the IWC (International Wheelset Congress) in Venice, Italy, in June by Alexis Ratier, the doctor of engineering who created this innovative method, the outcome of three and a half years of research.
Ratier’s technological advances are being developed further. In the years ahead, this will involve developing the use of these results in the context of digital simulations.
Today, the method has been validated on axles and tested on wheels. The goal is to validate its use on other types of railway parts. A research project will soon be proposed to meet clients needs even more closely.
Information reported by Alexis Ratier, test engineer specialised in analysing running gear failures and X-ray diffraction analyses at the Railway Testing Agency.