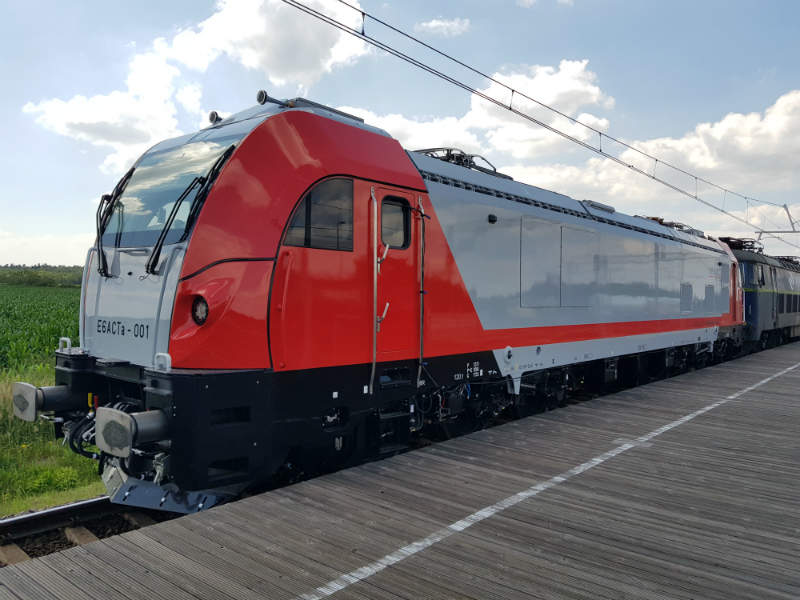
NEWAG has used MEDCOM’s latest SiC converters in Dragon 2 locomotives, which was presented on the tracks of the Railway Institute in Żmigród, Poland, on 12 July.
In September, it will be displayed at the Innotrans fair in Berlin, Germany.
The Dragon 2 locomotive was designed with heavy freight trains in mind and is the first 6-axle electric locomotive in Europe compliant with the Technical Specifications for Interoperability (TSI 2014), equipped with a level 2 ETCS. It is also the first Polish locomotive equipped with power electronics manufactured using silicon carbide technology.
Apart from the converters, MEDCOM also supplies the traction inverters and battery chargers for the Dragon 2 locomotive.
PSM-175 SiC is the largest auxiliary power converter in terms of power and the first one in Poland manufactured entirely using high-frequency technology. Silicon carbide transistors are installed both in the DC/DC converter block and in the inverter block. In order to make full use of their potential, the product additionally features fast 32-bit microcontrollers and high-frequency magnetic components, as well as proven signal processing algorithms. PSM-175 SiC also has an extended diagnostics and operating parameter recording system, and the communication module is equipped with Ethernet, CAN, USB, MMC, and RS232 interfaces.
Every Dragon 2 electric locomotive will be equipped with a set of Medcom’s two fully redundant converters with a power of 175 kVA each. In order to make optimal use of the liquid cooling system and the available space, the DC/DC converter blocks manufactured for Newag were mounted in the containers with the propulsion inverters, while the DC/AC converter blocks were installed in a separate container, where forced air-cooling was used.
“Thanks to the SiC power modules, new algorithms, and state-of-the-art processors and software, but also our engineers’ experience in optimising the mechanical design of the converters, we have created a compact product with efficiency as high as 96%. This is a value, which is impossible to achieve in similar products of this type based on silicon. We have reduced the weight of the system by about 400kg, decreased the dimensions of the magnetic components several times over, and at the same time minimised the system’s cooling requirements, which allows us to use smaller pumps, radiators, and fans,” says Piotr Wroński, vice-president at MEDCOM.
Apart from its compact design and high efficiency, PSM-175 SiC also displays high voltage stability (+/-5%). The product was designed in a way making it possible to adapt it to various output power supply source, including power supply from a combustion engine and generator. Thanks to that, it can be used in hybrid vehicles with a special combustion module for use on non-electrified route sections.
“We have been working on the development of the SiC technology for many years now and we are certain that it is one of the most promising technologies in the field of high-power power electronics. We are already able to use power electronics devices based on silicon carbide in every railway vehicle and electric bus out there. And I obviously mean products manufactured using full SiC technology, in which both transistors and diodes in the converter are made of silicon carbide. Modern electric vehicles require the use of ever smaller and lighter power electronics devices with even higher energy efficiency. SiC makes this possible,” says Piotr Wroński, MEDCOM.