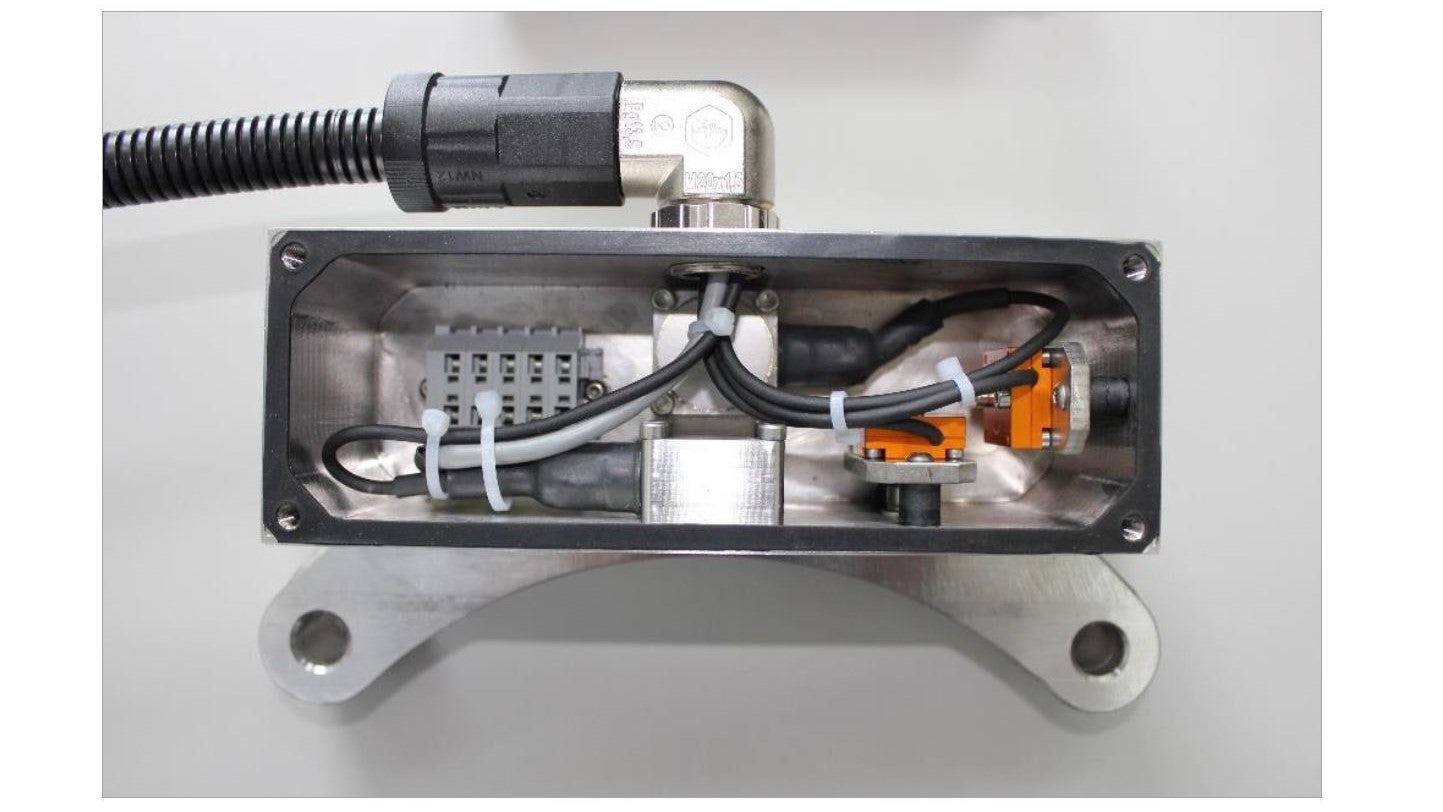
Railway infrastructure monitoring is cumbersome, disruptive and expensive. Or isn’t it? In partnership with Siemens Mobility Türkiye and DB Systemtechnik GmbH, Turkish State Railways (TCDD) decided to take an innovative approach: Continuous Infrastructure Monitoring (CIM). Enabled by ASC sensor technology, they are moving from a corrective ‘find and fix’ approach to ‘predict and prevent’: the proactive identification of future risks by integrating historic with real-time data collected through inertial sensors embedded in high-speed passenger trains.
Railway infrastructure monitoring needs to occur regularly, typically using special machinery that disrupts regular train services, to ensure that any signs of fatigue or other parameters running out of spec are detected early, so that critical infrastructure maintenance can take place in a timely manner and avoid costly breakdowns and service disruptions.
Increased capacity and ride comfort
TCDD wishes to maximise both the capacity of its railway network and passenger comfort while minimising service disruptions. To that end, the national Turkish operator collaborates with Siemens Mobility Türkiye and German rail infrastructure specialist DB Systemtechnik to equip a high-speed Siemens Velaro train with the latest innovative technologies to conduct all necessary measuring activities continuously in real-time.
“We’ve already been gathering extensive Continuous Infrastructure Monitoring experience on the German railway network,” says DB Systemtechnik head of testing services Dr. Lars Müller. “A critical success factor for CIM to deliver valid results is the use of the most robust and stable sensor equipment.”
“For this very reason, we have been relying on ASC Sensors, and they’ve never let us down,” recollects DB Systemtechnik senior engineer onboard infrastructure monitoring Dr. Klaus Ulrich Wolter. “At Deutsche Bahn, we’ve been conducting continuous monitoring from high-speed in-service trains since 2013.” The ICE trains used typically cover a daily average of 1,500km and the IC2 double-deck trains cover approximately 1,200km daily. Since 2018, ASC sensors have been in use. “In five years with almost three million kilometres covered by some of our CIM trains, ASC’s sensors are still running smoothly. It’s that reliability and the cutting-edge expertise of our partners that we are also offering to our customers, in Türkiye as well as around the world.”
Monitoring ‘where wheel meets track’
The CIM-equipped Velaro for Türkiye, based on an ICE 3M/F high-speed train manufactured for Deutsche Bahn, will be able to conduct comprehensive monitoring at speeds of up to 300km per hour and beyond. The sensors used are equally suitable in freight trains, long-distance passenger transport, and urban rail systems.
What counts, therefore, are the long-term robustness and stability of all sensors in use. “We need to position the highly sensitive equipment as closely as possible to where the wheel-track interaction happens”, explains Wolter. “To be able to do that and not have to replace sensors every other day, we can only work with the most robust components resisting significant mechanical forces, shocks, noise, temperatures, moisture, and more that keep delivering stable results over the long term.”
For this purpose, diverse ASC accelerometers and gyroscopes have been integrated in tailormade measurement systems. “To capture the most subtle deviations from regular train behaviours, vibrations, noise levels, centrifugal, contact, and other forces in this high-speed environment, all our inertial sensors have been embedded directly at the axle box,” explains ASC managing director Renate Bay.
Predicting the future
Longitudinal height is the most critical track geometry parameter. “It changes more rapidly than other variables of the inner track geometry and is of great influence on operational quality,” states Wolter. From the values measured by capacitive accelerometers of the ASC OS series, longitudinal heights are determined at intervals of 2cm independent of train speed. The maximum acceptable measurement uncertainty accumulated across sensors, amplifiers, algorithms, and other factors is 0.5mm according to EN13848-2.
“Other key parameters that our CIM system keeps monitoring include track twist, calculated from gyroscope signals, as well as dynamic alignment resulting from lateral accelerations,” says Wolter. The latter are also used to assess railroad switches and insulated joints while ride comfort is another important parameter established from these acceleration forces.
In all this, the DB Systemtechnik team needs highly accurate results. “Since once you start determining future maintenance needs, every little inaccuracy widens the window of uncertainty,” says Wolter. This is another reason why DB Systemtechnik partners with ASC, as even the smallest inaccuracies could trigger major uncertainties and, therefore, costs for the customer.
Innovating the Railway Networks
Ride comfort is another critical parameter established from the accelerations measured inside the passenger coaches. It is a key reason for railway operators, like TCDD, to implement CIM, as this will provide consistent data to meaningfully improve the passenger travel experience.
Passenger comfort is of particular relevance in Türkiye, as several high-speed lines are about to be completed and go into operation shortly. This includes a 1,213km line connecting the capital Ankara with the cities of Konya and Eskisehir, and another to Istanbul, measuring 533km.
Like any new train, all newly built rail infrastructure also has to pass a wide range of rigorous tests to get certified for public service. “The specially configured Velaro with latest sensor technology ‘on board’ will be utilised in the certification testing of these new high-speed rail lines,” reveals DB Systemtechnik head of onboard infrastructure monitoring Dr. Jörg Heland. In addition to local standards, they will meet Europe’s stringent Technical Specifications for Interoperability, a set of standards and requirements agreed between EU members, EEA, and associated countries to ensure compatible rail transportation across countries.
CIM reduces costs
“The beauty of Continuous Infrastructure Monitoring is that we’re now able to automatically monitor and proactively evaluate all components along the track, without having to delay or stop other traffic,” highlights DB Systemtechnik senior manager of business development and sales Dipl.-Ing. Yilmaz Tosun.
The advantages of moving from corrective to data-driven ‘predict and prevent’ maintenance are compelling. “To date, we’ve seen cost savings of up to 30% compared to the use of dedicated standalone measurement trains, in addition to significantly lower repair and maintenance cost and enhanced operational quality.”
For this approach to unfold the intended impact, DB Systemtechnik is able to fit all necessary measuring equipment onto any train. In addition to ASC’s inertial sensors, this also includes technologies for the monitoring of track bed density, overhead line condition, overall train operation, and various perception systems. “Today, the Velaro is not only the fastest, but also the most comprehensive measurement train ready for active service,” Lars Müller is convinced.
Applications are almost endless. “Based on the latest technologies and experience gathered with our flexible and reliable partners, we are able to turn nearly any in-service train into a fully equipped, automatic CIM train,” Jörg Heland says. “To ensure safe, sustainable, and productive railway mobility, we believe all infrastructure will be monitored this way in the future.”