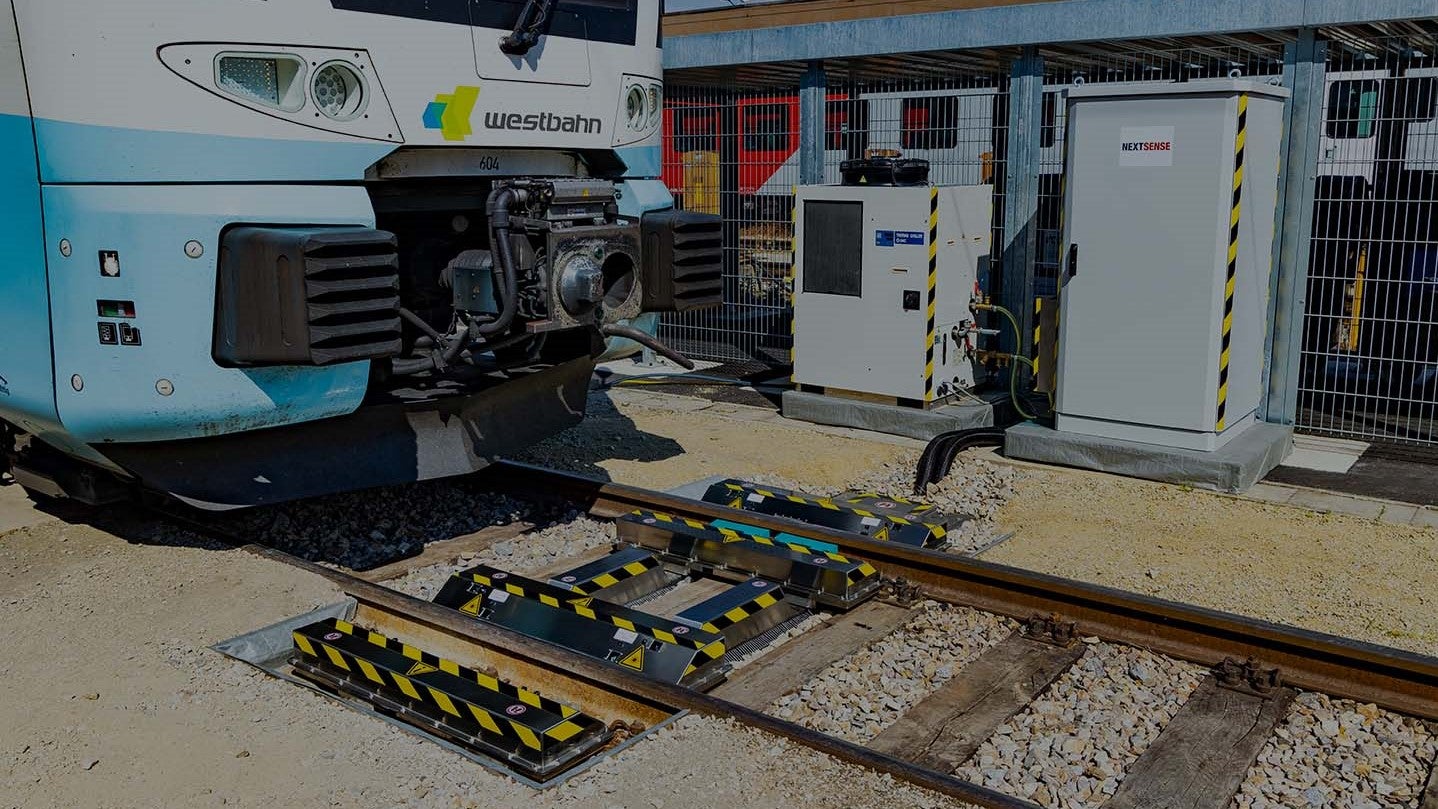
With the latest product CALIPRI X, together with CALIPRI Predictor, Hexagon introduces a ground-breaking, automated, permanently-installed solution for precise train wheel profile measurement and predictive maintenance.
Hexagon’s Manufacturing Intelligence division today announced the launch of CALIPRI X, a fully-automated, on-track wheelset measurement system that delivers significant productivity gains and operational cost savings to the rail sector. Combined with the analytical capabilities of the Cloud storage and analysis tool CALIPRI Predictor, CALIPRI X allows rail operators to safely run their trains with longer, more predictable maintenance intervals, less downtime, and reduced lifecycle costs.
Safety is paramount in rail. Regular wheelset measurements must be made to meet stringent safety requirements and ensure safe operation and passenger comfort. However, measurement of wheels and wheelsets is still typically performed manually, which is labour intensive, time-consuming and costly. CALIPRI X removes this need for manual measurement by effortlessly delivering precise results in seconds from an automated, permanently-installed, optical scanning system designed for 24/7 operation.
“We’ve really pushed back the boundaries with this integrated solution,” says Hexagon CALIPRI product manager Peter Lehofer. “It’s a genuine market first that meets rail industry needs for fully-automated wheelset measurement, without the sacrifices of precision and reproducibility that are commonly seen in products available today. The combination of highly accurate and reliable data, ease of use and the analytics provided by CALIPRI PRedictor will sabe our customers a lot of money and bring piece of mind as they maintain their roling stock over its lifecycle.”
With CALIPRI X, the measurement process couldn’t be simpler: a train drives slowly over a sensor unit where laser and camera modules automatically measure and record the profile of the wheels. The system measures all wheelset parameters according to the European standard EN 15313, including wheel profile, diameter, back-to-back distance, equivalent conicity, camber, and wheel toe.
The most important parameters and variables are known in seconds, and out-of tolerance areas immediately identified. Combined with CALIPRI Predictor, measurements are automatically and instantly stored in the Cloud and wear evolution is evaluated to enable planned downtime based on the as-is and forecasted condition of wheels, so unplanned downtime caused by wheel condition is eliminated. CALIPRI Predictor is an easy-to-use Cloud storage and analysis tool for CALIPRI measurement devices. The data is securely stored, highly available, safe to access and cost effective. By predicting wear levels, the maintenance schedule can be adjusted to the condition of the vehicles. This enables predictable and safe operation of the fleet.
The system is the latest development from NEXTSENSE, part of Hexagon’s Manufacturing Intelligence division. CALIPRI X builds upon Hexagon’s proven CALIPRI non-contact optical laser measurement technology. CALIPRI handheld devices are well-known and recognised across the rail industry for providing quick, exact, and reliable wheel profile measurement, with unmatched repeatability.
CALIPRI X is easily installed on existing tracks and is designed for 24/7 all-season operation. A rugged sensor unit with no moving parts ensures the system withstands the harsh railroad environment and requires minimal maintenance. Temperature compensation allows operation in any weather to ensure reliable results year-round. For the best productivity, the system is designed for installation on tracks where trains frequently run, such as in front of depots, workshops, washing facilities or in sidings. This allows frequent measurements to be made, without extra effort or costs. With no start-up delay, it is always ready to go. The solution ensures full traceability and allows secure 24/7 access to results and analytics for fleet technicians, workshop owners, maintenance workers, and other company personnel, wherever they are located worldwide.
Making more measurements means more data on wheel wear is available for analysis, allowing CALIPRI Predictor to accurately forecast wear levels.
Rail operators can plan their maintenance based on the wheelsets’ actual condition, allowing trains and entire fleets to be operated with longer, more precise maintenance intervals and less downtime, resulting in significant operational cost savings. CALIPRI Predictor ensures full traceability of measurement results and allows secure access to data and analytics for fleet technicians, workshop owners, maintenance workers, and other company personnel in the workshop, office, or even on the road.
Product highlights
Reliable measurement
- Proven CALIRPI measuring principles deliver accurate and reliable resutls every time
- Integrated temperature control and compensation allows operations in any weather year-round
- Highly sophisticated and efficient recalibration procedures
- Eliminates chance of human error, meaning less unplanned fleet downtime, safe operation of trains with longer maintenance intervals, and reduced lifecycle costs.
High availability of measurement results
- Designed for 24/7 all-season operation
- A rugged sensor unit with no moving parts ensures the system withstands the harsh railroad environment and requires minimal maintenance
- Long-term operation of system guaranteed
- No start-up delay: the system is ready for measurement all the time, anytime, meaning less system downtime, no need for manual backup measurements, saving time and effort, reduced labour costs, and increased maintenance efficiency
Connectivity and analysis: putting data to work
- CALIPRI Predictor enables the automatic sending of measured data and results to the Cloud
- Smart trend analysis of wheel wear with CALIPRI Predictor
- Remote system diagnostics and support give confidence and peace of mind and provide conclusive results available in seconds, immediately identify out-of-tolerance areas while condition-based and predictive maintenance allow extended maintenance intervals, resulting in significant operational savings